かんばん枚数の設定・計算方法|かんばんサイクルの1-1-1や1-1-2の意味とは
かんばんサイクルでいう1-1-1(1日1便、1便後納入)の意味を理解するためには、このかんばんを使った受発注システムの理解が必要です。以下にかんばん方式の基本的な考え方と、かんばん枚数の計算方法や設定方法について述べていきます。なお、トヨタ生産方式における「かんばん」は正確にはひらがな表記ですが、昨今はこの仕組みを使用する企業の裾野も広く、カンバンと表記されることもあります。
かんばん方式の実際|なぜ「かんばん」にメリットがあるのか
「かんばん」とは、トヨタの生産方式を支える仕組みの一つであるジャストインタイム生産方式には欠かせない道具であり、システムです。自動車部品は、数万点にも及ぶため、自動車メーカーへの部品納入は時間と場所が明確に決められており(そうしないと自動車工場のラインや倉庫がパンクしてしまいます)、特殊な大きさ・形状のものを除き、リターナブル容器であるプラスチック製等の「通い箱」を使って納品が行われ、この通い箱にはかんばんを差込むカードホルダーやかんばん挿しと呼ばれるポケットが箱側面についています。
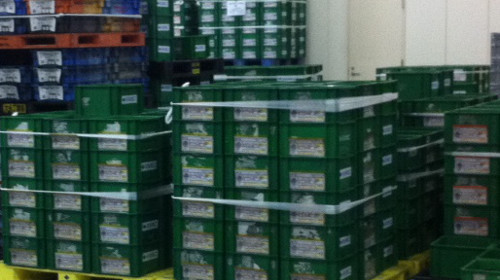
緑色の通い箱に「かんばん」が付けられて出荷を待っている状態
自動車メーカーの生産ラインにはこの通い箱ごと部品が運ばれていきますが、生産に使ったものは「かんばん」を外して、部品メーカーへ戻るようになっています。こうして各種の部品箱についた「かんばん」の着脱を行うことで使った分だけを部品メーカーへ発注を行い、部品メーカーはこの「かんばん」を製品の入った箱に取り付けて納入を行うことで成り立つのがかんばん方式です。
必要な部品を必要なときに必要な数だけ取り入れ、車の作りすぎという最大の無駄を省くためにトヨタが作り出した生産方式を支える仕組みといえます。
かんばんは必要な枚数を計算で設定してある
かんばん方式は、ある製品についてその「かんばん」総枚数だけ設定しておけば、発注する側も、受注する側も、返ってきた「かんばん」の分しか準備しないので、受発注の処理が簡便であり、大量の部品をやり取りする分野にはうってつけです。
また、この方法はかんばんが回転していく日数をうまく設定することで在庫自体がなくても、最小の労力で部品供給を可能とします。かんばん枚数を調整することで、部品メーカー側での在庫自体も最小にすることが可能になります。逆に言えば、発行するかんばんの総枚数をコントロールすることで、在庫自体もコントロールすることができます。
通常、欠品を防ぐよう基準在庫をもって運用する場合、自動車メーカー側からの毎月の使用予定数である内示は月ごとに変動しますので、その都度、基準在庫数の見直しを製品ごとに実施しなければなりませんが、かんばん方式の場合は枚数を調整することで、工程内の在庫も調整することができます。
この方法を使う場合、自動車メーカー側では部品在庫というものは基本、ライン側(ラインそく)と呼ばれる生産ラインのすぐ横(車に組み付けるためにすぐに使える状態にある場所)にあるか、受入と呼ばれるトラックが荷卸しして、ライン側に運ぶまでの間、仮置きされている場所にしかありません。これらはいずれも自動車の生産台数分しか置いていませんので、1日ではなく、時間が遅れただけで生産ラインが止まってしまうということになります。稀に自動車メーカー側の設備トラブル等が原因で予定の生産台数が作られないことがありますが、こうした場合には「納入ずらし」と呼ばれる納入時間のスライドが実施され、受入やライン側が部品在庫でパンクしないように調整がとられます。
かんばんに印字されている情報|実務では電子化されているかんばん方式
「かんばん」には部品の名称、個数、納入場所、メーカーなどの情報が記載され(QRコードで読み込めるようになっています)、納入者は広大な敷地にラインが複数存在する自動車メーカーのどの受入場所に、何時に納入すればよいのかわかるようになっています。
かんばんが使われ始めた当初は実際にかんばんの現物をもって部品メーカー⇔自動車メーカーの間を行き来していましたが、現在は大部分がeかんばん(イーカンバン)と呼ばれるシステムで電子化されており、部品メーカーはかんばんデータを専用の受信機で受信し(後工程発行)、自社で印字して製品を入れる通い箱にセットして納入する、という方法をとっています。受入を行う自動車メーカーサイドも、バーコードでこのかんばんを読み込みますので、かんばん現物自体を戻さない方法が主流になっていますが、原理はまったく同じです。外れたかんばんデータはシステムに取り込まれ、自動車メーカーから部品メーカーが持っているかんばん発行機へデータとして伝送されていきます。この際、感熱方式で印字を何度も繰り返しできるかんばんを「リターナブルかんばん」と呼び、使い捨てのものを「紙かんばん」と呼びます。
また客先である自動車メーカーへ納入する際に用いる「かんばん」のほか、自社の工程間を行き来するときに使う「工程内かんばん」も連動して使われます。
部品メーカー間やその仕入先との間でもかんばんでのやり取りを行い、こうしたかんばんは電子化ではなく、昔ながらの現物のかんばんを何度も使いまわす方式での運用が今も行われています。このように最終的に顧客がトヨタという場合、直接
かんばんは、製品を入れる通い箱ごとに1枚ずつ取り付ける
製品の入っていた通い箱から外された「かんばん」は、製品を運ぶトラックなどで一緒に運ばれ、出荷元に返される仕組みになっています。かんばんは無尽蔵に発行されるわけではなく、一定の枚数を発行し、手配増減に応じて総枚数を増やしたり、減らしたりしますが、これは「かんばん」が返却されてからどれくらいで製品が再度出荷されるかと、箱あたりの入り数、自動車の製造ラインで1日あたり何個必要なのかによって枚数が変わってきます。また、部品供給側でどの程度の安全を見るかによっても必要な枚数が決まります。
かんばんの枚数設定が肝
かんばん方式の肝は、このかんばんが戻ってから製品が出荷されるまでに必要なリードタイムを加味した「枚数設定」にあります。かんばん発行が電子化されてからも、たいていの部品メーカーではこの枚数設定機能をついたシステムを使いますので、枚数を変更することでかんばんが発行されるタイミングが変わります。多めの枚数にすれば、かんばんが外れると同時にかんばんがすぐに発行されますし、適正な枚数にしておくと、かんばんが戻ってから出荷までのリードタイムを計算した上でかんばんが発行されることになります。
かんばんの総枚数を設定しないとどうなるか
かんばんの枚数を設定しないということは、かんばん方式ではなく、普通の受注方式と変わらなくなりますので(単に注文書のかわりにかんばんが飛んでくる形です)、自動車メーカーからの毎月の内示をもとに必要な基準在庫を計算して、注文がきても納期通りに出荷できるよう準備しておくことになります。
この場合は、サプライヤーとなる部品メーカー側は、自動車メーカーから納期の何日前に確定手配が入ってくるかを逆算し、手配が入ってからの生産では多くの場合は間に合わないため、内示を元に必要な在庫を事前準備しておきます。
受注から生産、出荷までのリードタイムを想定して必要な在庫を持って運用することになりますが、手間がかかるという点を除けば、得られる結果というのはかんばん方式と同じになります。
ただし、最小の労力で最小の在庫での運用を行うことは難しくなりますが、製品の生産リードタイムによってはかんばん方式がもっとも効率的とはならないこともありますので、客先に対しては「かんばん方式」が指定されている場合、これに沿って納入しつつ、自社内の完成品にいたるまでの取り回しは、状況によりかんばん方式ではない方法を使うこともあります。このあたりは生産の実際を踏まえた上で運用方法を決めておく必要があります。
「かんばん」はトヨタだけ?
ちなみにトヨタとそのグループでは「かんばん」が使われ、これが製品のラベルのかわりも果たしていますが、他メーカーでも製品箱には指定のラベルを貼り付けて部品メーカーは製品を出荷することになります。マツダや三菱自動車であればJJラベルと呼ばれる製品ラベル・納品書を、受注時に各部品メーカー側で出力印字し製品の箱へ差し込んで出荷する仕組みになっています。日産自動車も独自のラベルがありますので、注文が伝送されてくると仕入先側で出力し出荷時に箱へラベルをつけて納入することになります。
ただし、大きな違いとして、かんばんの場合、その原理は使った分だけ、つまりかんばんが製品箱から外れた分だけを発注するという点にあります。また、ひとつの製品ごとに枚数が設定されていますので、在庫を抑制したり、安全を見て多めに在庫確保したりする機能が内在していることになります。こうした意味では、かんばん方式を採用しているのはトヨタグループとそこへ納入するメーカーだけということになります。かんばんと、出荷品のラベルは異なるものです。
かんばんサイクルの意味
前置きが長くなりましたが、かんばんサイクルとは、このように運用されている「かんばん」が運ばれた輸送便から何便後から出荷されるかを取り決めたサイクルです。
つまり、かんばんは製品の入った箱について移動していくわけですが、「かんばん」が外れてから仕入先へ運ばれ、また新しい製品とともに出荷されるまでのリードタイムが必要です。前述のとおり、自動車部品は自動車メーカーの生産ラインに時間指定で納入されますので、納入便も1日に何便もあることが一般的です。1日に何便の納入があって、そのうち、かんばんが運ばれた便から何便後に新しい部品が出荷されるか、を決めたものがかんばんサイクルであり、かんばんが外れてから製品出荷までのリードタイムでもあります。
かんばんサイクルによって、必要なかんばん枚数が決まります。この枚数設定を間違えると、お客さんが欲しいといっている時間までに製品の出荷が間に合わず、最悪の場合、自動車生産のラインストップという事態にもなりかねません。
かんばんの枚数を増やすことを現場用語では、「ぞうまい」(増枚)、反対に減らすことを「げんまい」(減枚)と呼びますが、月間の内示で提示されている受注の増減によって部品メーカー側ではかんばんの枚数をコントロールしていきます。
必要最低数のかんばん枚数にしておけば、自動車部品メーカー側は、最低の在庫で製品出荷することができますが、逆に多すぎると、出荷を待つ製品がかんばんがついたままの状態で自社の出荷場であるストアに滞留することになります。自社製品の生産リードタイムも加味してかんばん枚数を設定すると、かんばんが届いてから生産を開始するまでの無駄も極力抑えることができます。
また、いくら平準化生産といっても、客先からの手配はある程度内示からは振れますので、その分も安全に織り込む必要もあります。
4時間おきに1日に6便を使って自動車メーカーへ納入している例を見てみます。
下図の例では、6便のトラックが自動車メーカーと部品メーカーの間を行き来しています。部品メーカー⇒自動車メーカーの便には部品が積載されており、反対に自動車メーカー⇒部品メーカーの便には使われた製品の箱についていた「かんばん」が部品メーカーへ返却されるために載っています。
赤線で示す部分に、「かんばん」が載っており、かんばんサイクルが1-6-4とすると、「1日に6便のトラックが走っており、客先からかんばんを受領してから4便後に製品が出荷される」ことになります。したがって、以下の1便でかんばんを受領した場合、5便を使って出荷されることになります。
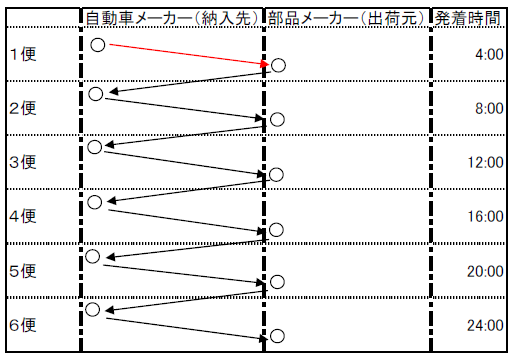
かんばん枚数の設定方法と計算式
各製品ごとにかんばんの枚数設定を行うには、かんばんサイクルに基づいた以下の計算式で行います。
必要な情報は、かんばんサイクル(1日何便走っていてかんばん受領後に何便後に出荷できるか)と、1日あたりに納入が必要な数量、1箱あたりに入っている製品数量(かんばんは通い箱の単位で付けられるためです)、安全値です。
安全値というのは、自動車部品の欠品というのはあってはならない事態でもあるため、たとえば、遅延のリスクや出荷あるいは生産時のロット単位を加味したり、内示に対する手配の振れを考慮してかんばん枚数を加算することになります。
企業ごとに明確な定義や計算式で安全値を決めているところもあれば、一律でいくつ、あるいは経験則や勘から割り出しているところもあります。要は、客先の日当たりの注文数(かんばんの振り出し数)が多少振れたとしても遅延や欠品を起こさない仕組みであればよい、ということです。
下図で示すとおり、かんばん回転枚数というのはかんばんの必要枚数でもありますが、1-1-1や1-1-2といったサイクルの指標と、客先への日当たり流動数、箱あたりの収容数で決まるということは、客先への日当たり流動数が上がった場合、下がった場合で、必要なかんばんの枚数が変わることになります。
このかんばん枚数の計算式で算出した基準よりも多めにかんばん枚数を持てば少し安全を見た運用が可能であり、基準どおりに持てば、無駄のない運用ができ、基準を割り込むと、欠品のリスクが高まるということになります。
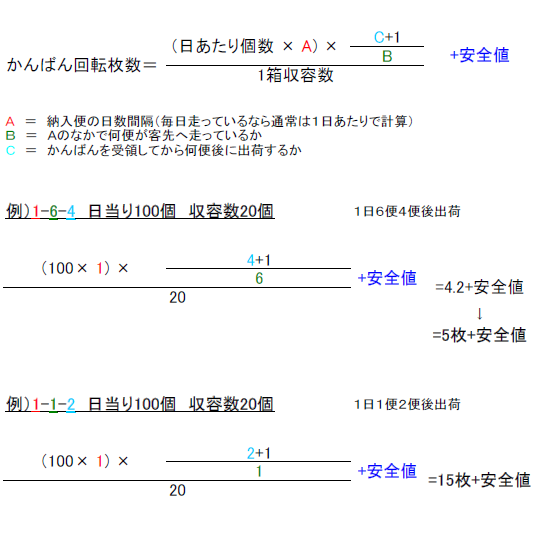
1-6-4の場合、1日6便、4便後出荷となりますので、1日100個(1箱20個入り)使用される上記の例では1回の出荷で5枚のかんばんが振り出されます。100個(5箱)納入されると、そのまま5枚のかんばんが外れて戻ってきます。戻ったかんばんが4便後に出荷されるのであれば、1日経過していませんので、翌日の手配100個の出荷に十分間に合わせることができます。手配振れや生産遅れがないとの前提であれば、5枚のかんばんだけあれば、1-6-4のかんばんサイクルの設定枚数としては最低限まわすことができる、ということになります。
対して、上記計算式の1-1-2(1日1便2便後出荷)の場合は、1日に1便しか部品メーカーから自動車メーカーへ納入する便がありません。加えて、2便後の出荷ということはかんばんが戻ってきてから3日後の出荷ということになります。同じ条件で1日100個(1箱20個入り)のオーダーが毎日入り続けるのであれば、1日5枚のかんばんが振り出されますが、かんばんが帰ってきてから出荷までにさらに3日かかります。最初に返ってきた5枚のかんばんは、返ってきた翌日のオーダー100個に使うことができません(3日後の出荷になってしまうため)。さらに翌々日に使うかんばん5枚もありませんので、上記の最低必要なかんばん枚数は15枚ということになります。
上記いずれも日当たり100個のオーダーが毎日来る、との前提での計算ですが、実際には100個の日もあれば、200個の日もあるということになるとかんばん枚数は足りなくなります。かんばんはオーダーを平準化する仕組みでもあるため、かんばん方式では日当たりの個数は乱高下しにくくなっていますが、まったく安全値を見ずにまわしていると欠品のリスクもあるため、安全値の部分で枚数を加算し、部品メーカー側では出荷に備えることとなります。
スポンサーリンク