BCP対策と調査の意味とは
BCPとは事業継続計画のことで、英語のBusiness Continuity Planの頭文字からきた略語です。簡単に言えば、自然災害や不測の事態が発生した場合に自社事業をどのように復旧させて継続していくかを策定した方針やバックアップ対策を意味しています。自社が使用するサプライチェーン網を含めた全体で策定していく必要があります。ここでは工場を保有する製造業の事例からこの制度の意味をわかりやすく紐解いていきます。
後述する通り、材料から製品として顧客へ供給するまでのサプライチェーンは川上から川下までつながっていますので、BCPもこの流れに沿って各所がうまく連携できないと緊急時の供給再開というのは覚束ないことになります。ありていに言えば、どれだけ自社で復旧が進んだところで、材料の調達ができなければ生産ができないためです。また顧客へ届ける輸送ルートの確保も必要です。
近年はテロ攻撃、社内ネットワークハッキング・クラッキング、事故等、自然災害に限らない「不測の事態」が増えており、サプライチェーン網がグローバル化し(一部部材の寡占化)、複雑化するにつれ、影響が広範囲の産業や企業に及ぶのも大きな特徴になりつつあります。放っておくと自社の事業・工場が止まってしまうような事態が一見あまり関係のないような事故や災害からも起きるということです。
BCP対策や調査を行う意味
BCPの対策一般には具体的な災害例・事業継続にリスクのある事例が想定されており、そうした場合にどれだけの被害が自社で発生し、何日後から復旧できるのかということが書かれています。
近年は特に水害や地震、火災、異常気象等の自然災害、戦争・紛争、不可抗力事由が要因のFM宣言、コロナによるロックダウン等事業継続に影響を及ぼす多くのリスクが顕在化してきていますが、様々なレベルでのBCP対策と行動計画の重要度が増しているとも言えます。
仕入先やサプライチェーンの川上で突然FM宣言を行い、部材の供給が寸断されるというようなことも起きやすくなっています。これはサプライチェーン網が複雑化、グローバル化していることとも無縁ではなく、どこか知らない国で起きた災害がいきなり自社の生産に影響を及ぼすということが現実的に発生しうる世界になってきているということでもあります。
取引先からBCP調査依頼というものを受け取る機会も増えてきていると思います。これは、客先・納入先から見れば自分たちが生産に使用する部品や材料が不測の事態が発生したときにもきちんと納入できるのか、あるいは納入復旧にはどれくらいかかるかを調べるためのもので、客先の調達部門や購買部門が窓口となって仕入先(サプライヤー)に定期的に調査をかけるものです。一方でその客先にしても、その先の客先から同様にこうしたBCP調査依頼を受けていることが多々あり、サプライチェーンの川上−川下までつながってくる話ではあります。
自社内対策、部品調達、客先対応の3層構造
BCPには会社全体での方針や総論をまとめたもの、事業部門単位での方針をまとめたもの、工場単位や個々の製品ごとにバックアッププランを策定したもの等、いくつかのレベルのものがあります。
また自社の経営層やリスク管理部門が中心になって自主的に策定するものと、客先からの要望に応じて提出するものとがあります。前者は災害時の影響の評価や方針をはじめとした全体的なものが多いですが、後者は供給している製品や個品ごとに提出するものもあります。
上記2つに加え、自社で使用する部品や材料、燃料等の製造にかかせない様々な物品、資材を調達している仕入先に対しても、BCP調査を行い、緊急事態発生時にどのように調達が可能か、代替方法があるかを事前に調査しておく必要がありますので、こうしたBCP調査もあわせて行う必要があります。
これは輸送網についても同様で、トラックや鉄道での陸送がどのように行うことができるか、海外拠点が関与するのであれば、船便やエアー便等、どこの港や空港からの搬出・搬入が可能かといった検討もあわせて行う必要があります。
まとめると、以下3つの階層での対応が必要となるのがこのBCP対策の要諦となります。
- 1.自社のBCP対策と方針
- 2.客先へのBCP調査依頼に対する回答調査
- 3.自社の仕入先へのBCP調査と対策
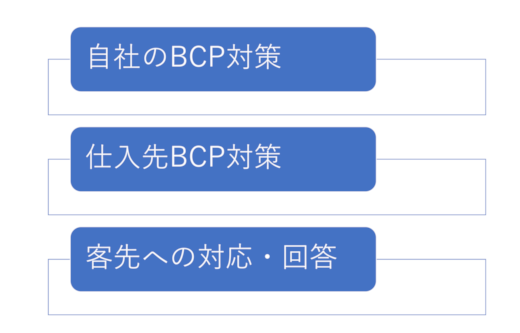
社内のBCP対策
自社が策定しているBCP対策や方針というのは基本的に詳細は非公開です。株主や取引先などのステークホルダー向けに公開されているものは、安心させるための材料として行っているもので、あまり詳細な部分は公開されていません。具体的なBCPになればなるほど、設備・人員の詳細情報をはじめとした機密性が高い情報が多く含まれるためです。
具体的な想定災害に対して、社員のどれくらいが死傷し、何人がいつまでに出社できる状態・連絡できる状態になり、建屋や種類ごとの設備保有台数、生産や受発注に使用する基幹システム、ライフラインがどのような状態になっているかの想定が決められており、そこからどのように復旧させていくか、どういう組織が司令塔になるのかといったことが決められています。
前述した通り、この対策は全社、事業部、工場などの単位で行われるため、階層的な構造になっていることが多いです。
この策定には社内関係部門の協力が不可欠ですが、仕入先への調査結果も内容に加味させる必要があります。
どのレベルのものまで作るかというのは会社によりけりで、非常時の組織体制や連絡網のみで終わっている場合もあれば、具体的なバックアップスキームや、工場間の支援体制まで踏み込んでいるケースもあり、一概にはいえません。後述する客先に対するBCP調査回答というのは、正直、自社方針がなくても、如何様にも回答できてしまうため、形式的に行っているだけの場合もあります。ただ、近年の緊急事案発生件数を見れば、BCPやBCM(Business Continuity Management。BCP策定・導入・改善などを包括的・統合的に行う事業継続のためのマネジメント)がない状態での経営というのは、かなり危険なものと言わざるを得ません。
明文化されたものがなくても、緊急時に指揮を執る管理層の頭にはどのように対処すべきかの青写真やポリシーがあるケースも見受けられます。
企業によっては供給不安等が起きると専門の部会や特別な会合が招集され、経営層の指示で関係部門が集められ、その都度対応を検討するタイプのところもあります。BCPそのものにこうした対応をうたうこともできますし、併存も可能です。
客先からのBCP調査回答依頼
一方で客先や納入先からくるBCP調査依頼というのは、大きく取引先(サプライヤー)としての調査と、個々の製品としての調査に分かれます。前者は、建屋が耐震基準に則ったものか、水害や火災に対してどのようなリスクがあり対策があるかといったいわゆる仕入先管理の一つとして実施されるもので、全般的な質問や回答を求める内容が多いです。
一方頻度の面からも最もよく実施される製品単位のものは、客先から自社が供給している対象品のリストが送られてきて、それぞれの製品についてBCP対策をどのようにしているか回答を求めるものになります。この場合、他の工場での生産ができるか、在庫がどれくらいあるか、復旧にどれくらい時間かかるかといった点が焦点となります。
何等かBCP対策などやっていなくとも実は回答はできてしまいますが、取引先によっては特定の選択肢を選んだ場合、別途対策計画を提出するよう要望されることもあります。
複数の工場を保有している会社であれば生産技術部門等の協力を得て、設備の互換性やバックアップ対応可能性、同一品生産の有無などを調べることで、バックアップ生産という回答も可能です。
自社の仕入先へのBCP調査と対策
これはちょうど前述の客先が自社に実施するのと同じように、自社もその仕入先に実施して部材の安定調達体制を担保するという意味合いの調査です。
自分たちも適当に回答できてしまうことからわかるように、仕入先もこれは同様で、小さいところで災害に対する備えがない工場や会社は多数あります。
代替調達先を事前に検討したり、二社購買などでリスク分散をはかることになりますが、この辺りも実際に起きてみないと何ともいえないというところです。発生時には調達部員が仕入先へ現況確認に行き、場合によっては自社が支給している金型や貸与している設備を急ぎ別の生産先へ移動させる措置をとる必要性が出てくる可能性もあります。
多回納入をはかる必要がある自動車部品などの業種では、下請先や仕入先がひとつの市内や県内に集積していることが多々あります。これは輸送費を削減したり、納入にかかる時間短縮をはかったり、緊急時の特便輸送をおこったりという側面では有利にはたらくのですが、ことBCPの観点からは非常に不利になります。
熊本や東北の地震の例でも代替先がないために停止しており、その会社の復旧を急ぐ以外に再開の方法がない例が発生しています。
供給できなくなった場合の実際の対応
災害時の対応方法について社内である程度決めていても、実際に発生してみないとどのようになるか分からないというのが正直なところかと思います。したがって計画には複数のもの、代替案も必要ということになります。
中国で工場を操業しているメーカーの多くで経験したのは、同国のロックダウン政策によって製造がままならない状況になったり、あるいは製造ができても出荷ができない、従業員が出社できない(自宅待機)、輸出・輸入に制限かかる等の事態です。
このときは、ロックダウンされた中国の工場から設備・治工具の運び出しもできず、製品の迂回輸送にも多大な時間を要し、バックアップ計画がその工場から何らかの運び出しを伴うものになっていた場合、機能しなかったということになります。
早い段階で、部材調達も含め中国以外の工場で生産しバックアップするという方法が有効ということになりますが、これがBCP対策の段階で考慮できていたのかという点がひとつのポイントです。
また連動してコンテナの世界的な不足が起き、海上輸送費用の高騰や船の予約ができないという事態も発生しました。
このときのサプライチェーン運用の側面からは輸入国側である程度の在庫を持っておくことと、方針や政策の違う複数の国からのバックアップ生産をどれだけ早くできるかというのがポイントとなります。在庫で客先への欠品を防いでいる間、他国の工場でのバックアップ生産の準備を特急で進め、そこからの調達段取りを行うという方法です。この場合、状況により、日本からその工場へ資材や部材を次々に送り込む必要もあります。
これだけ広範に発生したコロナ問題でも、ロックダウンの状況や輸送網の状況というのは国や地域で大きな違いがありました。このため、グローバルで製造を展開している会社であれば、例えば本社等で全拠点で製造している同一品や互換性のある品物の状況を把握できたり、バックアップ生産ができる製品や工場の組み合わせを事前に登録・管理できていれば動きも早まります。
右往左往することになるのは、現地の状況が刻一刻と変わり、情報収集もタイムリーにできない状況という限られた環境のなかで、バックアップをどうするかという選択を迅速に決めなければならないという点があるからです。
リソースは限られていますので、中国のこの工場のこの製品をインドに任せるという選択をした場合、インドの工場もキャパには当然制限がありますので、他の工場分の引き受けには制限がかかります。ある製品は在庫がまだ持つので、復旧までの時間は稼げると判断してバックアップ生産をしないという選択もときには必要です。こうした判断を限られた情報と時間のなかで行うことになります。
BCPのなかである程度の方針や考え方の共有ができていれば、その時に入手出来ている情報をもとに判断の迅速化や検討事項の抜けや漏れを防げる可能性はあります。
工場や製造業でのBCP対策例
客先のBCPへの回答や自社でのBCP対策で検討すべき事項というのはおおむね以下のような内容となります。
工場の立地条件は各種災害に対してどのようなリスクがあるか、評価されているか
工場や倉庫が活断層の上にある、あるいは水害が起きやすい地域にあるというようなことを事前に評価しているかどうかという点です。また人災やテロ攻撃等に対する評価も同様で、設備やインフラ網がどのような影響を受けるかをあらかじめ想定しておく必要があります。
災害に対して備えのある建屋や設備か
耐震性能や集中豪雨、河川の氾濫などの水害、電力不足、悪意のある第三者からの攻撃等に対してどのような備えがあるかを検討するという内容です。上記のリスク評価とあわせて、自社の建屋や設備がどれだけのことに対応可能か、脆弱性はどこにあるかを見極める内容となります。
同じものを作っている工場があるか、その工場の生産キャパは不測の事態にどれくらいの期間で上げられるか
バックアップ生産拠点の確保とそれにかかる対応を決める部分です。同一品が作れるといっても、生産キャパもあわせて確認が必要で、どこまで無理が効くのか、どこまで能力を短時間で上げられるかの評価を事前に行うという内容です。
複数の工場で作ることができる場合、どのような条件で生産が可能か。設備や金型・治工具、どれらの部品等を送る必要があるか。
これも上記と連動しており、設備や金型・治工具自体は自前ではなく別工場からの輸送やチューンナップが必要という場合はそれらの対応可否やリードタイムも調べておく必要があります。
設備の復旧や生産の再開がどれくらいでできるか
災害等で止まってしまった工場の設備復旧・生産再開がどれくらいで可能かを評価する項目です。これには災害の程度によって大きく変わるので、いくつかに段階を分けて策定しておく必要があります。設備が少し動いたのか、設備は動いていない、あるいは設備が倒れて何かが破損しているのか、といった状況ごとにどれくらいで再開できるかを試算したものとなります。
部品や材料の調達がどれくらいでできるか
これは生産再開とも連動する項目です。生産に必要となる部材がどれくらいで入手可能かを評価・検討するものです。仕入先に対するBCPも連動しています。代替候補先や、代替材料、代替部品の検討もあわせて行っておく必要があります。
部品や材料の在庫がどれだけあるか
生産できなくなった場合に製品在庫でどれくらい間供給できるかを示す指標となります。もっとも簡便なBCP対策なのですが、倉庫が災害で倒壊してしまったり、製品の保管棚が転倒したりといった場合は、在庫品がだめになってしまうこともあります。また在庫場所自体が水害や火災でやられてしまうこともあります。リスクを考えるなら、複数の場所での在庫ということになります。
自動車部品のBCP
製造業のうち自動車産業(部品)から見たBCPについて最後に簡単に触れたいと思います。BCPを考える上で自動車部品の大きな特徴としては以下があります。
- 自動車メーカーからの発注から納入までのリードタイムが短い
- 納入頻度が1日1回〜数十回等、多回納入になる
- 注文や内示データが頻繁に飛び交い、計画変更も多い
- 客先側での在庫は原則持たない
- 客先の近くにデポを設けてタイムリーな納入ができるようにしている
- サプライチェーンが階層構造をなしており裾野が非常に広い
- 自動車の生産を止めるわけにはいかない
- 客先となる自動車メーカーは海外拠点を多数持つため、部品メーカー側も海外進出が進んでおり、複数国に工場を持つ
多くのTier 1メーカーでは外資系を除くと「不測の事態」が発生しても材料メーカーのようにFM宣言をほとんど出さないということが挙げられます(もちろん致命的な問題により供給不能になった場合は別です)。自動車の生産には3万点前後の部品が要りますが、これをある程度のモジュール、かたまりにまとめても相当な数になります。何かが欠ければ、自動車の生産ラインが止まり、他の部品メーカーへの発注もすべて止まります。
下図の通り、多層構造になっているのが自動車部品のサプライチェーンで、どこかが止まれば自動車の生産ができないということになります。これもあって、BCP調査の依頼と回答のやり取りは各層で頻繁に実施されています。
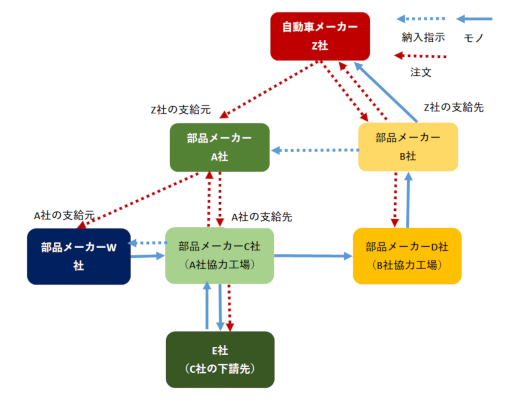
もっとも、階層が下に行くほどに、複数工場を持っている割合は下がっていき、災害に対応できるよう離れた地域や国に工場が割合はさらに下がっていきますので、在庫での対応(もちろん倉庫がやられてしまえば在庫もないのですが)と復旧までの時間を工夫して努力します、というのが大半のBCP調査の回答となってしまいます。
自動車部品メーカーの視点からすれば、お客様である自動車メーカーのラインを最初に止めるのが自社であってはならないという強い意志があり、あらゆる手段を駆使してラインをつなげようとします。時には採算度外視でサプライチェーンをつなげようとします。費用をかけても何をやってもできないということがないよう、下請先や協力工場を多数使っている場合、それらひとつひとつにつきある程度のバックアップ先の候補を決めておく必要があります。これは自社の海外拠点も同様で、リスク情報をキャッチしたらバックアップに向けて指揮をとれる部署が社内にあるということになります。
加えて、自動車部品というのは流動数が多く、自動車メーカー側では特殊なものを除くとほとんど在庫しませんので、工場での車両組付けの時間にあわせて多頻度で納入するという商習慣があります。したがって、生産するサプライヤー側でも商社でもない限り、多量に在庫するということは不可能に近いというのが実情です(量が多すぎて倉庫がパンクする)。
このため、この納入に何としても間に合わせるよう、手を尽くすのであれば、別工場でのバックアップ生産を早期にとれる状態に持っていく必要があります。
もっともこうした対応に対し、一部の自動車メーカーは部品メーカーに対して対応に要した特殊な費用をあとから負担するという場合もあり、単なる契約関係では割り切れない心情的なものがあるのも大きな特徴と言えるかもしれません。
契約書通りに運用するなら、部品メーカーは供給再開できるまで所定の手続きに則ってFM宣言をして納入遅延の責任や損害を免れるということになりますが、それをしない代わりに、エクストラでかかった費用を自動車メーカーが一部肩代わりする(契約にはそのようなことは当然記載ありません)ということも発生しています。
自動車メーカーに直接納入する部品メーカーでは、複数拠点での生産によるバックアップというのが最も現実的な方法で、グローバルに展開する会社の多くはこの手法をメインにBCP実務を組み立てています。
スポンサーリンク